Increasing the efficiency of electric motors by using high-precision myTec
expansion technology
Our customer is a well-known manufacturer of electric motors. During the production of electric motors, sheet metal stacks (stators) must be aligned as precisely as possible for welding. The manufacturer uses expansion technology to achieve this.
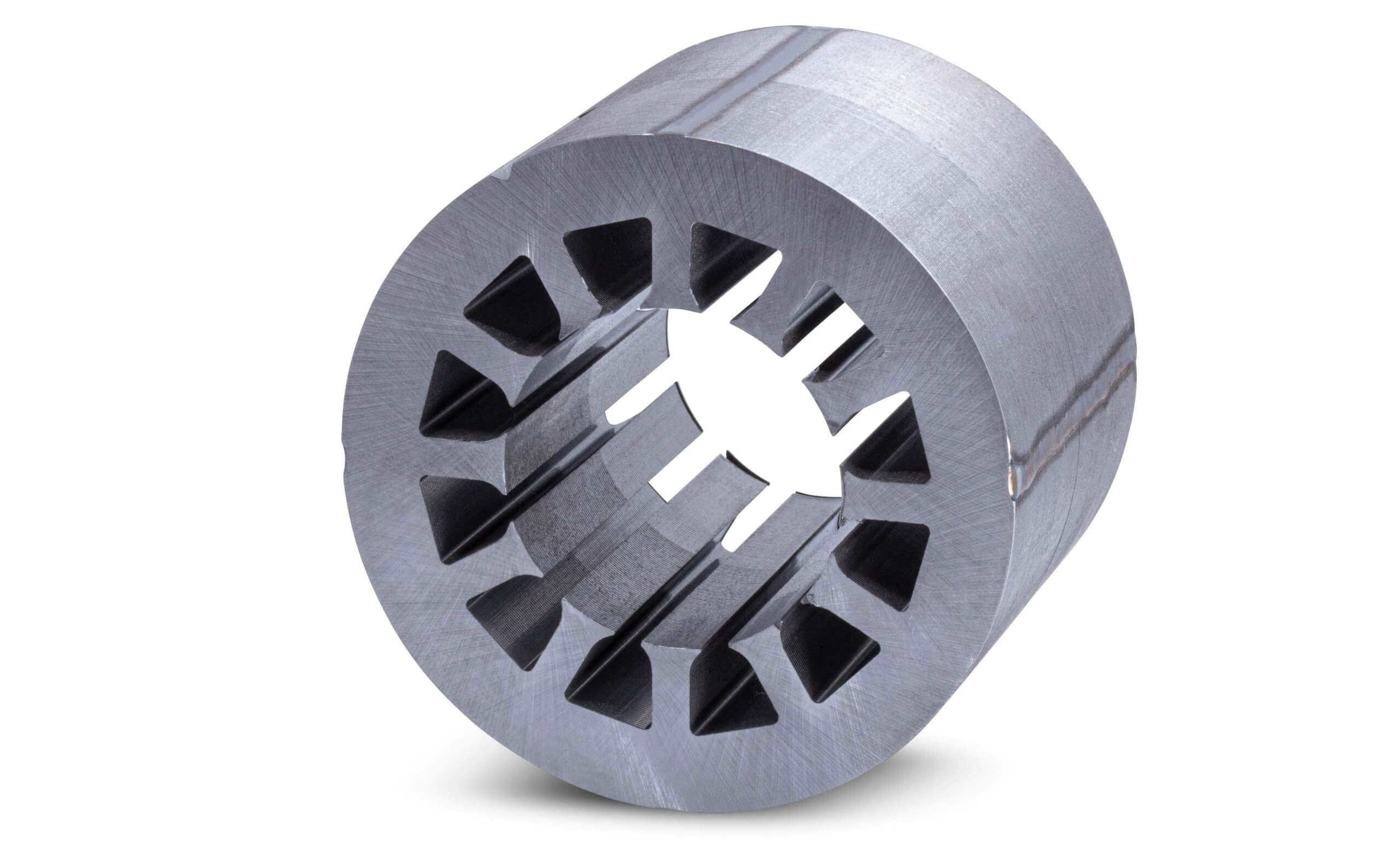
The next machining process step is to machine the bearing seats of the motor housings with pressed-in stators. For this purpose, it must be taken up and tensioned in the bore of the stator by means of expansion clamping technology.
In order to increase the production efficiency of the motors and reduce scrap, the customer wanted to use extremely precise clamping systems that could achieve the greatest possible accuracy (roundness and concentricity) of the stators to the bearing seats to enable more exact positioning of the rotors in the assembly of the electric motor.
The customer decided on myTec expansion technology because these hydraulic expansion mandrels allowed the stator packs to be centered and aligned with the highest precision. The former mechanical mandrels, on the other hand, were not reliable, as the alignment of the stators cannot match the same precision as compared to the myTec hydraulic expansion clamping technology.
In the first step, the specific design of the expansion arbors was agreed upon with the customer. The configuration was then tested in trial runs and successfully used in the customer’s production. Due to the high precision of the myTec hydraulic expansion clamping technology used, the laminations on the stator can now be positioned with high accuracy and the distance between the stator and the rotor can be significantly reduced, resulting in higher efficiency and a longer service life of the motor.
By using myTec expansion technology, the customer is able to increase productivity and reduce manufacturing costs. At the same time, product quality is increased and production is more efficient.